Got myself a J-Head MK-IV Hot End clone, from Ebay (snipermand), to see if it will be good enough to replace my heavily modified Mendel Parts Hotend V9 clone; and since the J-Head MK-IV is a clone, this is my quick review to share my purchase experience. The review also includes an illustration of how the different components fit together, how the J-Head clone stacks up against the original J-Head and conclude whether Hot End clones are really worth considering.
The J-Head MK-IV will be the third Hot End clone I’ve purchased in the last 12 months with the hope of putting together a decent extruder system for 1.75mm PLA filament. The Hot End I’m using right now is not as good as it should be and it’s a Mendel Parts V9, the first clone I purchased, which I had to heavily modify due to a manufacturing or design error made by the supplier in India. The second clone I purchased was the MBE Extruder V9 from qu-bd.com, and like for many other users, it just would not work with the 1.75mm PLA filament. This Hot End kit is a Makerbot Stepstruder clone.
J-Head MK-IV Hot End Clone Design
The illustration above shows the clone version of the J-Head MK-IV Hot End and looks similar to the original J-Head supplied by hotends.com. The version I have is with the aluminium nozzle/heater combination which is also available in brass (J-Head MK-IV-B). The overall machining quality of this nozzle is very good and was delivered with the main components pre-assembled, and has some kind of red sealant locking the peek insulator on to the aluminium nozzle/heater. A resistor, thermistor and some wire was included, and also wire insulating PTFE tubing and bootlace ferrule connectors; which all needed assembly.
The peek nozzle holder has perhaps gone through the most evolutionary changes during the life of the J-head which demonstrates the importance of cooling; and version four is used here, but with only four vents instead of the five as per original design. The extra machining to the peek nozzle holder has greatly increased the surface area to allow heat to dissipate more efficiently to allow better cooling for extruding PLA filament. The series of vents round the peek nozzle holder would allow a cooling fan to be effective at lower RPM speeds making the 3d printer much quieter during operation.
The aluminium nozzle/heater combination that make the J-Head, is probably the best and most reliable 3d printer Hot End design in it’s price range. You have what is commonly three separate components (nozzle, heater block, threaded tube), combined into one. With the machining required to produce the nozzle and peek nozzle holder together, it still manages to be the best value for money Hot End out there; with the important good usage track record. The aluminium version I have is based on the blueprints for nozzle/heater combination version one.
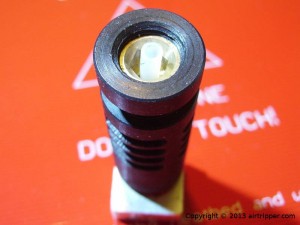
J-Head MK-IV Converted to 1.75mm with PTFE Tube pushed down through the melt chamber to the nozzle tip.
PTFE liner tube is used in the peek nozzle holder which is held between the nozzle and the set screw under pressure. The design uses the PTFE tube to create a good seal between parts and also provide an almost instant transition from cold end to hot end for the filament path. The PTFE liner also provides some heat shielding from the peak nozzle holder as well as the nozzle itself, however, some active cooling would be required for PLA filament to prevent the PTFE liner from heating up too high. An extra PTFE tube was supplied as a method to convert the J-Head to a 1.75mm extruder from it’s native 3mm design; a method not supported in the J-Head Wiki because the melt chamber is machined for 3mm filament and not 1.75mm.
J-Head MK-IV Clone v J-Head MK-IV
If I’d done my research properly I might have decided to get the J-Head MK-IV from hotends.com instead of getting it from RepRap.me through Ebay. With the various clones available, you just can’t be sure that they’ve been manufactured using techniques that achieve the kind of precision and quality you would find in the original item. Basically, these Hot Ends are sent out to customers untested, and when ordering a clone Hot End, you are putting a lot of trust in the supplier, their understanding and knowledge of the product, and the quality of manufacturing.
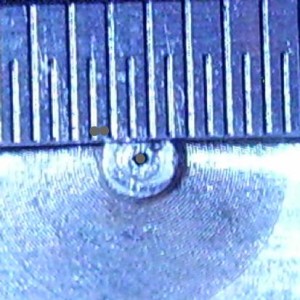
J-Head MK-IV Clone. View of a Poorly drilled orifice that was claimed to be 0.4mm and turned out to be 0.5mm
Had I done some research on the J-Head MK-IV Hot End I would have realised that the 3mm to 1.75mm conversion method, applied to the J-Head clone, is not recommended. The conversion involved inserting another PTFE tube inside the existing PTFE liner; as shown in the above illustration. The PTFE tube is used to reduce the melt chamber diameter size to 2mm. It’s not clear how well this conversion performs or whether there are maintenance issues.
The 1.75 mm J-Head version from hotends.com would have a melt chamber machined for 1.75mm filament (rather than being reduced with PTFE tube from 3mm), which is likely to improve reliability over the Hot End clone version and have better control over to temperature in the melt chamber.
Hot End Purchase Experience
As I noted earlier, I’ve purchased three Hot End clones in the past 12 months with the third purchase being the J-Head MK-IV clone from RepRap.me via Ebay (snipermand). I ordered the J-Head MK-IV Hot End with a 0.4mm orifice and everything looked in order on delivery, the build quality looked good as far as I could tell and it seemed like I made a good purchase. However, while working on the J-Head, to get it ready for extruding, I kept noticing the Hot End orifice looking a bit big for 0.4mm. So I took some close up pictures with the nozzle tip up against a ruler and added some reference points to the Hot End nozzle images with an image editor. The image above right shows the grey reference points added.
The reference points on the image was used to accurately gauge the size of the Hot End orifice against the ruler, the orifice size appears to be 0.5mm in diameter. To confirm the size of the Hot End orifice I found an electronic component with 0.5mm leads, confirmed with calipers, and I was able to insert a lead into the orifice with a snug fit.
I’ve since sent a message to RepRap.me about the issue and still waiting for a reply. As it stands now I’m unlikely to use the nozzle since it does not meet the specification I wanted, and also unlikely to order another clone as this is the third clone failure to meet the specification claimed. Most people that order Hot Ends may not consider checking the nozzle size because the orifice is so small and take it on faith that they have been sent what they’ve ordered
Hot End Clone Conclusion
The J-Head MK-IV has few parts, but a lot can still go wrong through poor quality manufacturing and poor assembly. Things like poorly tapped screw threads, PTFE liner not retained properly, PTFE liner ends not cut squarely or cleanly, nozzle orifice drilled larger than specification, and assembly errors caused by lack of product knowledge. It only takes a single fault to cause the nozzle to fail and in view of this, it would be better to put your trust in the original designer and supplier.
All in all it was a bad decision to purchase this Hot End clone due to the lack of backing from the supplier. The sale campaign was mostly backed up with a copy and paste from the J-Head Wiki; with an added thermistor table for only the Sprinter firmware. The thermistor supplied had no brand or type to identify it and would be difficult for the less than average 3D printer user to set up correctly in firmware. Also, the supplier did not declare any working experience or manufacturing process to back-up the reliability or build quality of the their Hot End clone design.
A 3d printer Hot End is what makes a printer a 3d printer and so is a critical component that needs to be right. So the advice would be to buy your Hot Ends from the original designer and manufacturer that is backed up with good documentation and support. Basically, if you are out to buy a J-head Hot End, get the J-Head from hotends.com. Supporting the original designer/manufacturer/supplier will help with further Hot End research and development.
[bodyadsrich1l]
Hi Mark,
Another great article.
So you are still using the V9 clone? Looking at the suppliers mentioned, it is difficult to work out who makes what and what is a clone and who is the originator.
What went wrong with the MBE extruder? I assumed that would be OK ( as it seems most of the RepRap work that way) instead of the Bowden tube ( which has it’s own set of problems). I thought the Bowden system would reduce the carriage mass and hence faster printing, but I’m firmly stuck at 20-25mm.
I’ve updated my extruder ( airtripper, of course) with a MK7 steel cog and it has much improved the situation; no more shredded PLA filament. Excellent!
William
I’m still using the V9 clone and is working a lot better now I’m using the MK drive gear pulley. The bowden cable set up is working great and I don’t feel it’s a disadvantage in view of the print results I’m getting now. My print speed is about 30mm/s and 60mm/s travel with 0.8mm retraction.
I think when selecting a hot end, it might be a good idea to get the opinions from those on the RepRap Forums before buying. I’ve noticed that some of the long experienced experts are still sticking to 3mm filament; I think the hot ends are more reliable for this size.
I’ll be doing a review of the MBE extruder after more tests. The reason I’ve had problems with it is that it does not prevent PLA from swelling in side the tube. The PLA filament jams quickly after being stood for a few seconds.
Mark
You experience with snipermind is about on par with mine – these are Chinese clones, and are not very well made or machined. The first one I received the PEEK tube had numerous mis-starts on the drilled holes, and had been milled inaccurately. Mine also had an extra “cooling” cut, as it appears yours does as well.
There is also no retention ring at the top to retain the PTFE liner. To be fair to snipermind, he did replace the PEEK tube, and I did keep the hotend – it’s sitting around if everything else breaks.
I ended up stateside, so picked up a 3mm and a 1.75mm version from Brian @ hotends.com. As usual and as expected, the quality is stunning. I just wish I’d picked up two of the 1.75′s – I want to play with dual extrusion!
FYI – Not sure if you’ve tested one, but the QU-BD extruder is not very reliable and I don’t recommend it at all. That said, a couple of folks have identified a couple of the problems, and it looks like you can at least use it as a decent extruder. Nothing short of replacement will fix the cone slope on the orifice, however, so if you ever crash it into your bed it’s done..
Unlike the J-Head clones, your version from hotends.com will be properly engineered for 1.75mm filament.
I had already got the QU-BD MBE extruder before discovering the bad reports being made against it. As far as I know, it just fails on PLA extrusion. I believe the extruder works fine with ABS filament.
The MBE extruder hot end is nicely engineered and I think it would have worked better with PLA filament if the nozzle tube was polished on the inside like the Prusa’s new all metal hot end.
Aluminum have twice better thermal conductivity then brass:
http://www.engineeringtoolbox.com/thermal-conductivity-d_429.html
and aluminum has smaller density then brass.This mean that aluminum is much better for hot-ends.The clones can be better then originals with respect to the materials.
Then 0.5 mm or 0.4 mm I cannot see big difference. you are lucky because your hot-end did not brake as my from a EBAY a polish cloner PTFE cold-ended one did break. Thats because of the PTFE is bad for ABS it deform and finally breaks. I have now a new J-Head MK-IV Hot End Clone from the same mentioned Ebay (snipermand) person. It looks very small. and 40W power heater at 12v is very good if compare with the original resistor 5.6 ohms 25.7 W@12V or 6.8 Ohms 21.17W@12V. I hope that this will not break.
this is from the
https://www.hotends.com/index.php?route=product/product&product_id=88
Internally, the filament path is identical to that of an already proven design.
The design is simple as the number of custom machined parts is kept to a minimum.
If necessary (and for 3mm hot-ends only), the PTFE liner can be replaced by using an off-the-shelf piece of PTFE tubing.
The PTFE is not stressed nor used to provide support. This reduces a point of failure that is part of other designs.
A resistor is used as a heater. There is no need to wrap nichrome wire or to bake a heater core.
Heat transmission is improved as there is no thermal junction where a separate heater screws onto the nozzle.
Included
Assembled J Head MK V-BV Hot-End.
Power Resistor, 5.6 ohm or 6.8 ohm (depending upon availability)
Thermistor, 100k, 3%
PTFE Insulation for the resistor and thermistor
Thanks Mark, I appreciate the article.
I bought an MK-IVB a while ago and am now installing it in my first printer. It is machined for a 3mm filament, but I also tried converting it to use 1.75mm with some PTFE tubing… I’ll let you know how reliable I find that to be.
One question regarding the hot end: I thought I fully installed the resistor into the board (RAMBo) properly, but when I try heating it up the hot end just remains at room temperature. With the MK-IV, are we supposed to declare thermal settings differently in Marlin, or keep it like:
#define TEMP_SENSOR_0 1
as the hotends website suggests?
Any help would be much appreciated!
Kevin
Hi Kevin,
Personally I would not use thermistors that has not been properly identified by the supplier as with the case on my J-Head purchase. I think the recommendations that hotends.com makes is based on the kit that they supply and test.
To make sure you get the temperature reading as expected it is best source your own thermistors that match those in the firmware configuration list. The following link is a type I use and I believe hotends.com has just started recommending the same:
http://www.rapidonline.com/Electronic-Components/GT-THERMISTOR-100K-3-61-0452
#define TEMP_SENSOR_0 1 should be enough to get your hot end heating up as long as you are getting an ambient reading from the thermistor.
I’m not familiar with the board you are using but defining TEMP_SENSOR_0 1 should enable extruder heater 0. One common error to check for is the power input cable; making sure it’s connected to the correct power input socket.
There is not really a lot to do to get the heaters going on the extruder and the heated bed, It’s just a case of good wiring connections and setting thermistors in firmware and of course choosing the correct motherboard configuration.
It will be interesting to see how you do with the MK-IVB.
Good luck with your first printer,
Mark
Thanks for fielding the question, and the suggestions. It turns out I was looking in the wrong place – the firmware was fine, but I had made a simple wiring mistake… good thing I didn’t ruin the board (yet)!
As expected, I ran into issues extruding after trying to convert to 1.75mm using PTFE tubing. Still working on it, but having the dimensions properly machined would (of course) be the best solution. We’ll see if I can make do on my limited budget.
Hey Mark – I’m getting back into the 3D printing scene after dropping out of it for a while after buying a SUMPOD around the same time you did. I never got mine running unfortunately. I’m considering picking up a J-Head to replace the stock hot end on my printer that gave me nothing but problems. The bracket that you have your mkiv clone installed on – is that available somewhere?
Thanks for all the info you put up here, it’s very helpful!
Hi Tim,
Some parts did spoil the Sumpod, the extruder just was not up to the job. I’ve printed about 6kg of plastic so far with the updates I’ve made and the printer is still going strong. I plan to change the X and Y carriages for much lighter versions for faster and better quality printing.
I can send the files for the J-head bracket but I guess you will have difficulty printing your own without access to a working printer. The bracket is untested but as long as the bowden cable is long enough not to pull on the fitting it should work fine.
If it will help you out, I can mail you the bracket I’ve printed to get you started.
Mark
I am definitely without a a working printer currently. I just recently backed a delta printer on kickstarter, but I won’t get mine until December at the earliest (boo). I appreciate the offer for your bracket, and I might take you up on it.
The folks at SUMPOD are sending me one of their newer hotends, but this will be the second one they shipped me (the first one never showed up). Hopefully it’ll arrive and I’ll be able to at least get it running, if only to print out some upgrades like a new extruder and hotend brackets.
If you could email me the files (or make them available somewhere) for the bracket I’d appreciate it. If I can’t get to the point that I can print them myself, I’ll let you know. Thanks again!