The Direct Drive Bowden Extruder V3 BSP Edition was first introduced on Ebay back in March 2013, followed by public release of all the design files in August. So to avoid confusion, this article is the documentation for the above extruder and not a new extruder release. While the bowden extruder continues to be popular it seems important to produce some documentation for it, even if only to provide some sort of version history.
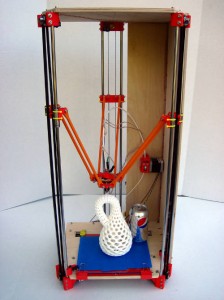
Rostock (delta robot 3D printer) fitted with Airtripper’s bowden extruder
About The Airtripper Extruder
The Airtripper’s direct drive bowden extruder for 3d printers has been a large success, which has allowed makers & builders to easily add an extruder to their custom 3d printer. Its simple bracket design means the extruder can be attached to most surfaces and T-slot type extrusions, and its compact design easily allow for multi hot end set-ups. The bowden extruder’s popularity was especially boosted when it was used on the first Delta Robot 3d printer called Rostock by Johann C. Rocholl. The Airtripper’s bowden extruder was originally designed to replace the Sumpod 3d printer extruder.
After writing the “3D Printer Extruder Filament Drive Gear Review & Benchmark” there is no longer any doubt about the capabilities of direct drive extruders when using recommended stepper motor and drive gear. With better stepper driver tuning, the MK8 drive gear could probably push more force than what I’ve recorded, and if you are only going to be using 1.75mm filament then a direct drive extruder is all you need for most 3d printing operations.
Available On Ebay
The Airtripper’s Bowden Extruder V3 BSP Edition is sold on Ebay by me as a kit with plastic parts and fittings, with optional PTFE tube and extra BSP fitting. The extruder kit is also offered without the plastic parts which allows the purchaser to get the bits from one place in needed quantities and 3d print the plastic parts themselves. My Ebay listings.
Additions & Tweaks
The latest batch of additions and tweaks was driven by requests to adapt the extruder to accept a BSP push in fitting. Other makers had successfully adapted the extruder to accept a type a of push fitting, but I wanted to use the most popular and most widely available push fittings and made my own adaptation. So the bowden extruder can now be fitted with the 1/8″ BSP 4mm straight fitting.
The second addition to the extruder, after the BSP socket add-on, is the pipe bracket. The pipe bracket allows a 4mm tube to be connected to the extruder so that filament can be gently guided from the spool to the extruder. A separate tube bracket, the new additional part, is used to fix the other end of the tube near to the filament spool. The tube bracket was a separate add-on with the last extruder version but now the tube bracket is integrated in the latest extruder body design.
Some tweaks was made to the extruder fixing bracket so that it 3d printed more neatly; you can use the Thingiverse STL viewer to compare this extruder version to the last version. Another tweak was made to the idler housing. It was found that the idler housing was prone to cracking when printed with brittle filament. So the tweak included widening the idler housing and thickening the walls; this has led to a shorter axle. The axle now drops to rest into a deeper sockets so that once the axle and bearing is pushed into position the axle does not constantly push into the idler housing walls, reducing stress and cracking over time.
3D Printer Bowden Extruder – Parts
Four 3d printed parts are required to complete the bowden extruder plus an optional part called the tube bracket. The tube bracket allows for a PTFE tube, or other 4mm outer diameter tube, to fit between the bracket and the bowden extruder; this allows the extruder to pull filament from the spool, guided by the tube, from different possible spool location around the printer.
3D Printing The Parts
Skeinforge had been my first choice for printing the bowden extruder parts for some time but Cura has shown to do a better slicing job – and much faster too, and with the ability to print a tray of parts one part at a time, means Stringing is kept to a minimum. I have used Slic3r in the past and found that the extruder body thin walls don’t fill correctly, however, the latest Slic3r versions may provide better results.
I’ve 3d printed the bowden extruder using only PLA filament and can’t really comment on how well the extruder parts will print using other filament materials. There have been reports that ABS filament works well enough but there have been a couple of reports about issues with printing the idler bearing housing correctly.
A print layer height of 0.25mm is always set with my own extruder parts print, with top and bottom layers set to 0.75mm. The fill density is normally set to 25 percent, and with the print speed set to 24mm/s, all the parts will take around three to three and a half hours to print.
Non 3D Printable Parts
A full description and quantity of the parts that are shown in the image above:
- 1 x M3 x 25mm S/S Cap Screw Allen Bolt.
- 2 x M3 x 30mm S/S Cap Screw Allen Bolt.
- 2 x M3 x 45mm S/S Cap Screw Allen Bolt.
- 1 x M3 x 6mm S/S Button Head Allen Bolts.
- 1 x M3 x 10mm Screw
- 4 x M3 Stainless Hex Full Nuts.
- 2 x M3 washers.
- 1 x 22mm of 1/4″ 6mm id Rubber Diesel Hose Tubing Line.
- 1 x 608 ZZ [8 x 22 x 7] Roller Skate Ball Bearings.
- 1 x 1/8″ BSP Male to 4mm Straight Push In Pneumatic Fitting
The above parts are required to assemble the bowden extruder to the stepper motor and allow for the bowden tube to be attached. If you own a Dremel type tool you can cut the 6mm and the 25mm screws from the longer versions if desired.
I’ve continued to use the rubber tube as the idler bearing pre-loader because it allowed for plenty of space to remove the idler housing from the extruder for filament changing. I’ve tried using springs and it was difficult to get the springs over the idler housing hooks.
Caution needs to be taken when fitting the BSP fitting to avoid splitting the extruder body. The threads on the BSP fitting provide a good grip inside the fitting socket on the extruder, so there is no need to tighten the set screw too much. The set screw only needs tightening just enough to hold the fitting in place.
3D Printer Bowden Extruder – Recommended
Since this is a bowden extruder, you will almost certainly be using a length of PTFE tube between the extruder and the hot end. The extruder is designed to take PTFE tube (4mm OD x 2mm ID) and 1.75mm filament, 1/8″ BSP Male to 4mm push fitting is used to connect the tube to the extruder.
As shown in the picture above, to avoid snagging when loading new filament, it is recommended to taper the end of the tube which can be done with a drill bit. Some snagging will occur occasionally but changing the PTFE tube alignment inside the fitting with one hand while loading the filament will help get the filament through the connector.
Before loading new filament into the extruder, straighten the end of the filament as much as possible so the end of the filament does not snag inside of the BSP fitting. Snip the end of the filament if not cut square.
Along with a high torque stepper motor, the MK8 drive gear is recommended for the direct drive bowden extruder. As shown in the tests here, a good stepper motor / drive gear combination will provided plenty enough torque to drive 1.75mm filament. It will be difficult to solve 3d printing problems or even to calibrate the printer properly without the correct stepper motor and drive gear behind the extruder.
The stepper motor I use with my own extruder set-up is the SY42STH47-1684B (Holding Torque (Kg.cm) 4.4) and you will find this stepper on the RepRap NEMA 17 Stepper motor Wiki page.
Due to the grip provided by the MK7 and MK8 drive gear filament pulleys, it is no longer necessary to have the extra bearing on the stepper motor axle. The MR105ZZ Ball Bearing was previously used on the axle to take some load of the stepper motor internal bearings, but since the MK7 and the MK8 drive gears have excellent grip on the filament, it is not necessary to apply a heavy load on the axle with the idler bearing. These same stepper motors are used to drive pulley belts and may put a higher load on the axle than the extruder idler bearing itself.
Airtripper’s Direct Drive Bowden Extruder V3 BSP – Files
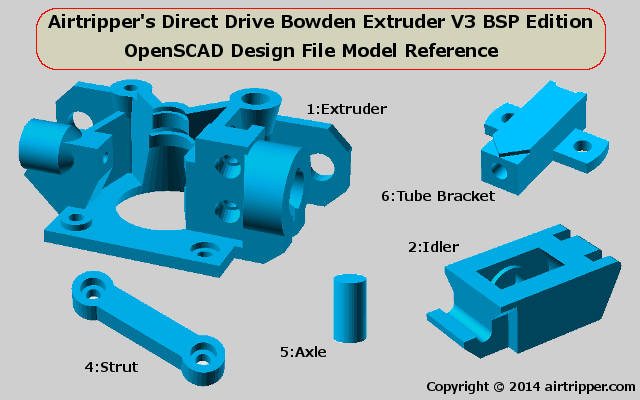
OpenSCAD Script File Code Snippet: preview_part = 1; // [1:Extruder,2:Idler,4:Strut,5:Axle,6:Tube Bracket]
However, should the STL files need to be compiled again, the OpenSCAD script file for the extruder is also available for download. At the minimum, you would only need to change one line of code to compile an STL file for each of the bowden extruder parts.
preview_part = 1; // [1:Extruder,2:Idler,3:Idler with brim,4:Strut,5:Axle,6:Tube Bracket,7:All Parts]
You’ll find the above line of code in the OpenSCAD script file at the top of the page after a few lines of comments. Basically, to select a model to edit or compile to STL, change the number assigned to the preview_part variable with the number assigned to the model; the image above shows a number assigned to each bowden extruder part model.
File Downloads
[bodyadsrich1l]
Related Articles
3D Printer Extruder Filament Drive Gear Review & Benchmark
Airtripper’s Bowden Extruder V3 – Updated Design
3D Printer Surgery #4 Extruder Upgrade Part 3
Airtripper’s 3D Printer Direct Drive Bowden Extruder V3 BSP
Is there a reason you specify the SY42STH47-1684B over the more commonly used Kysan 1124090 Nema 17 Stepper Motor? The holding torque on the Kysen stepper is listed at 5.5kg.cm vs the 4.4kg.cm listed for the stepper you spec.
My application is a Mini Kossel using your extruder and a 1.75mm e3d hot end with .4mm orafice. Any input/suggestions are appreciated.
Hi Emilio,
The SY42STH47-1684B stepper motor is basically used as a benchmark for high level of performance, all the bowden extruder performance graphs I’ve produced in previous topics are based on this stepper motor.
Any stepper motor type that match or better the specification of the SY42STH47-1684B should provide a reliable direct drive 3d printer extruder. The SY42STH47-1684B can serve as a starting point when looking for a stepper motor for direct drive extruder.
It looks like you have already got a good set-up, I think if you get any problems at all, it’s likely going to be at the hot end side.
Mark
Mark,
Thanks for the information. Not yet having purchased steppers for my build, which would you suggest I go with? The cost difference is minimal and my goal is to minimize potential faults and attain the best possible print quality.
As for the comment about the hotend, have you had a negative experience with the e3d or do you mention it because it is far less tried and true than the ubiquitous j-head?
Emilio
Emilio,
In choosing a good stepper motor I would start with the RepRap Wiki, the large choice available should help find a supplier closer to where you live. I think you can just divide the holding torque by 10 if you prefer Kg-cm over N-cm.
http://reprap.org/wiki/NEMA_17_Stepper_motor
If you have a good drive gear and stepper combination, the point of failure of the extruder is more likely going to be at the hot end, basically, I’m referring to any hot end; not just the E3D.
I only use PLA filament due to being able to print directly on to glass, so the J-Head MK5 hot end is perhaps the best choice for me. Personally, I wouldn’t buy an all metal hot end just for printing PLA.
Mark