Sometimes technological developments are born out of necessity—you have a need, you fill it. But other times technological developments trigger new needs and ideas altogether.
Read MoreAdditively Assists Your Additive Manufacturing
A startup company hopes to simplify connecting with and selecting a 3D printing service provider for industrial parts.
Read More
Uncovered: 4 AXYZ’s Secret 3D Wood Machine
For some time now we’ve been hearing rumors of a mysterious “wood machine” from a mysterious company called “4 AXYZ”. Now we know a lot more about it.
Read More
The Project That Wouldn’t Exist Without 3D Printing
We ran across a new product that apparently would not have happened were it not for the availability of 3D printing technology.
Read More
Ultra-Fast 3D Printing?
A surprise announcement from ORNL and Cincinnati Incorporated hopes to revolutionize 3D printed manufacturing. But how?
Read More
Confirming the Other Half of 3D Printing
The science of 3D printing was conceived some 30 years ago with intentions of becoming a new form of manufacturing. By 2014, that’s clearly happened. But after attending the opening event of NYC’s first 3D Printshow last night, we have another thought.
Read MoreSculpteo’s Factory Button
- See the entire batch of items as it will be produced inside the printer
- Get a better price by optimizing the positioning and spacing of your items and instantly see per-unit pricing
- Use any of three finishes (glossy varnish, satin polish and double polish)
- Adjust the orientation of models to ensure correct strengths
- Preview a simulation of each layer of your print to ensure everything is correct
Lulzbot Simplifies Life for a Mouthguard Manufacturer
What Does A Big Company Do With 3D Printing?
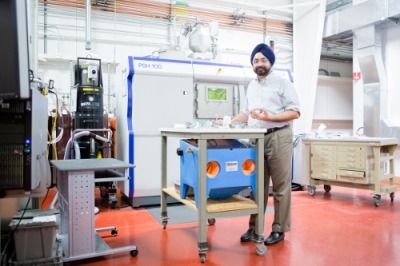
- GE has over 300 3D printers, covering almost all 3D printing processes
- Equipment from many different manufacturers are employed
- Most 3D prints are for research purposes, although there is recent investigation into 3D printing production airplane components by 2016
- Their focus is to try to reduce the number of steps involved in creating a component by leveraging 3D printing's ability to print arbitrarily complex objects
- GE requires 3D print materials not currently offered by the manufacturers in order to go forward with their plans
- They're seeking ways to 3D print electrical components, like "resistors, inductors and capacitors"
- Metal printed parts are almost strong enough for use, but GE requires a much better surface finish
It is in manufacturing where 3D printing can make the greatest impact. In speeding up company’s product development, letting them do more iterations and letting them do shorter run parts it can speed up their business as a whole. It is in manufacturing where serious money will be made either by vendors or companies that outcompete by using 3D printing in their supply chain.
Battle of the 3D Printer Manufacturers
U.S. Losing its Edge in Additive Manufacturing?
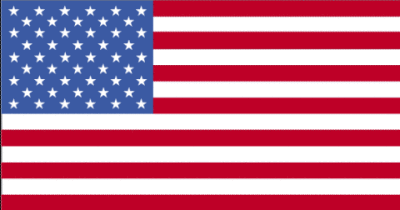
Manufacturing in 3D Printing's Future?
Advanced Manufacturing Seminars
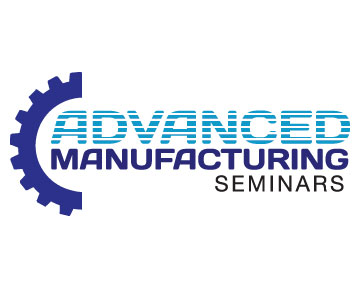
Knocking off a few Gas Stations...
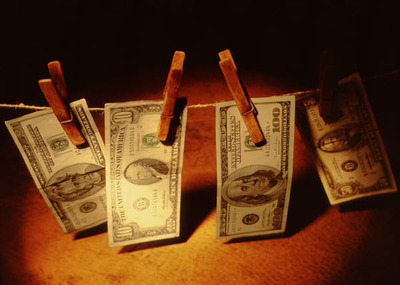
How Will 3DP Affect Your City?
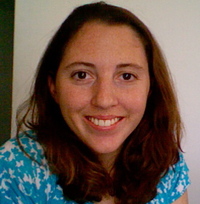
China Concerned About 3D Printing?
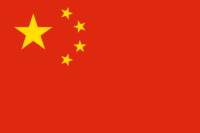
Such manufacturing is being enabled by the long march of technology. And it surely worries China. While economic historians remind us of the importance of the twin innovations of free markets and financial structures, both those factors pale against the power of technology to create productivity, and thus the wealth of the world.If the future factory is a machine born of emerging technologies and requires de minimus labor, on average such factories will be located preferentially where the skills and culture exist to invent and implement. And, on average, you’d put such factories close to demand.
Additive or Subtractive?
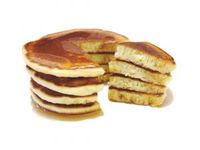
Specialized 3D Bikes
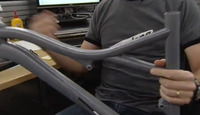