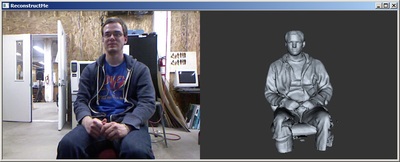
If you've ever been shopping for a 3D scanner, watch out for the price tag. Many commercial units providing high quality results and convenient features are well beyond the pocketbook of almost every hobbyist, upwards of USD$50K in some cases.
Are there less expensive methods of 3D scanning? Several 3D Scanning kits or hobby versions exist, but there are compromises in function and you'll still be short hundreds or even thousands from your wallet. Meanwhile, there is one way to begin 3D scanning and it's possible it may cost you absolutely nothing!
That method is ReconstructMe, a software tool we've
written about previously. Today we've been hands on experimenting with the tool to see how it works.
ReconstructMe is software that uses the commonly-available Microsoft Kinect 3D sensor to produce full 360-degree 3D scans. While other Kinect software exists, the ones we've seen tend to take a still 3D image from one location. ReconstructMe is quite different in that it lets you image the backside of the object as well as the front. In fact, you can scan all sides continuously to produce a true, full 3D model.
We took time in our lab to test ReconstructMe to experience its installation and use.
We found the worst part of the ReconstructMe experience to be software installation. The tool requires several drivers to be installed as well as a Microsoft framework. If that doesn't tell you something right away, we'll say it: ReconstructMe runs only on Windows machines.
If you run Linux or OSX you don't have a chance. Even using virtual Windows is not acceptable, as virtual machines frequently don't forward the required information as expected by ReconstructMe. We found only one example where someone had successfully
installed ReconstructMe on OSX using specific virtual machine software, but even then it did not work well due to performance limitations.
Our advice: read the installation documentation very carefully. Then read the documentation again very carefully and follow it precisely.
ReconstructMe really needs a good video card to work well because the software attempts to use the processing power of your graphics card to handle the scan data to produce the 3D model in real time. It is possible to use ReconstructMe without the graphics processing boost by scanning first and producing the model later, but this is awkward as you're never sure your scan truly covered the entire object as you can't see what you're scanning. ReconstructMe provides a
handy list of graphic cards to check compatibility and performance.
One problem we encountered with the installation had to do with software drivers. Each time we plugged in the Microsoft Kinect sensor, Windows would conveniently install the wrong drivers for us automatically. We had to rapidly cancel this frustrating auto-installation to enable a manual installation of the correct drivers.
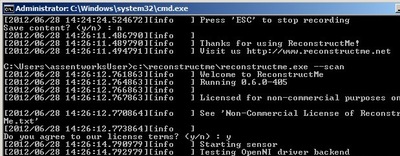
Once you've successfully installed the software, using ReconstructMe is relatively easy, even though it uses a command line interface that would likely frighten non-technical users. A single command launches ReconstructMe and you're presented with a two-pane window with one view being the live camera and the other the 3D model under construction.
Performing the 3D scan could not be simpler. You simply sweep the camera view around your object (which must be contained within a one meter cube facing the sensor when it is activated) and gradually complete the scan. You must look for "holes" in the generated model and repeat area scans to fill them in. Smooth, slow motions seem to collect the best 3D information. If you (as we often did) move the sensor too close to the subject for the Kinect to resolve (400mm), you'll receive an annoying BEEP. Or three. Too many beeps seemed to freeze the scan, but you could still save your results at that point.
An alternative approach is to place your object (or person in our case) on a rotating platform (or office swivel chair as we did) and slowly rotate them in front of the stationary Kinect sensor. ReconstructMe scoops up the data and magically produces the 3D model in front of your eyes. While this approach seems easier, you still have to pick up the sensor to manually scan areas not seen by the sensor while rotating (the top, for example).
The quality of the scans is relatively good. It's hard to measure this, but our experimenters thought the accuracy was in the 3-5mm range. Perhaps this could be increased by more careful and slower scanning. In any case, it's good enough to grab a 3D model of a person without keeping them longer than they'd become annoyed. It is not good enough for anything small, however. Jewelry scans would be impossible with ReconstructMe, as we suspect the Kinect is simply unable to resolve such details. The Kinect doesn't scan clear objects as it seems to see right through them. Similarly, it gets confused by complex fine details such as fuzzy hair.
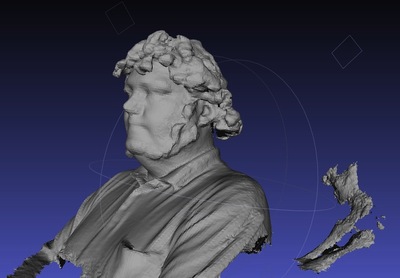
ReconstructMe can save the generated 3D model in several formats including OBJ and STL. Our experiment involved STL, which was produced correctly. We found the scans to include stray data, suggesting you should be careful where you place your subject - avoid nearby items. Be careful not to capture stray arms from an assistant rotating the swivel chair, as we did in this image. There were a few small holes in the model, but these were very easily corrected with 3D model management software such as NetFabb. More than likely you'll scan more object than you need; the table or chair your object rests upon will also show up in the scan. This necessitates some 3D editing to remove unwanted portions and close off the bottom.
ReconstructMe is available in two forms: Commercial and Non-Commercial. The non-commercial license is available at no charge, meaning if you already have a USB-capable Microsoft Kinect, this could cost you absolutely nothing to try! On the other hand, if you require a commercial license, you'll need to pay €360, or about USD$450.
For rudimentary 3D scanning of large items this price can't be beat, even considering the installation complexities and user interface peculiarities. We recommend you give ReconstructMe a test today.