I’m getting the hang of Eagle, and the design for the first Polarshield is close to being complete. Matt Venn is charitably helping me by gently pointing out the stupid stuff I’m doing. Luckily for me, the board is electrically very simple, being an aggregation of other designs rather than something truly original.
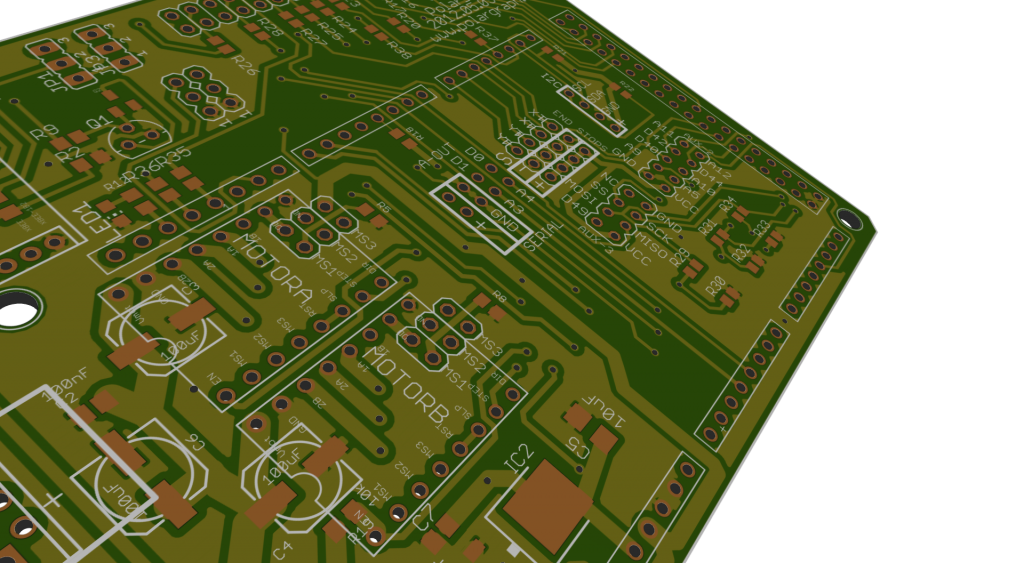
The polarshield is be the key piece of the PolargraphSD machine. It’s a shield with:
- 2x Stepstick / Pololu A4988 sockets.
- ITDB02 2×20 pin LCD touchscreen header w/ SD slot.
- XBee socket.
- 2x Servo motor connections
- 4x Endstop connections
Connected to a MEGA, then you can use everything all at once, on-board. If you don’t have stepsticks yet, then you can stack your existing Adafruit motorshield on the top, and it’ll work. This includes the touch-screen that will allow fully untethered drawing, and potentially some really nice things eventually.
Connected to an UNO, you can use your old Adafruit shield, or upgrade to use stepsticks. Using stepsticks frees up the SPI pins on your UNO, so it could, in theory, read an SD card too. (SD reading isn’t likely to become part of the UNO build for the foreseeable future, but it could be hacked to do it for someone who is determined.) You definitely can’t use the LCD screen though with the UNO.
The XBee port is accessible to both UNO and MEGA, so if nothing else, this can be used as an XBee breakout that will cooperate with a motorshield.
There are connectors for endstop sensors that will eventually provide for automatic calibration, but there’s no hardware to go with that quite yet. I’m currently thinking of little magnets attached to the cords and some reed switches or hall effect sensors positioned just above the sprockets. This needs to be built and thoroughly tested, but I don’t actually think there’s much to it. It was never planned to be part of the PolargraphSD design, so I’m not rushing into it with only a couple of weeks to go.
The board is largely based on the RAMPS board that folk use in their Repraps, so there’s a handful of other pins broken out by default. I have tried to be good and group pins together, and the board does have a slight general purpose quality to it for that reason. Hopefully it should be open to extension without too much hacking. Pics and plans soon.